APPLICATION:
HF Alky Heat Exchanger
LOCATION:
Chicago, Illinois, USA
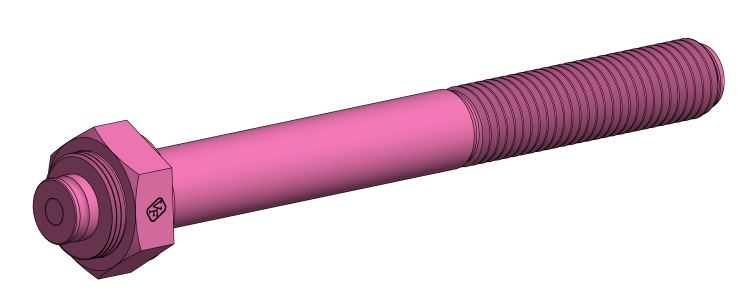
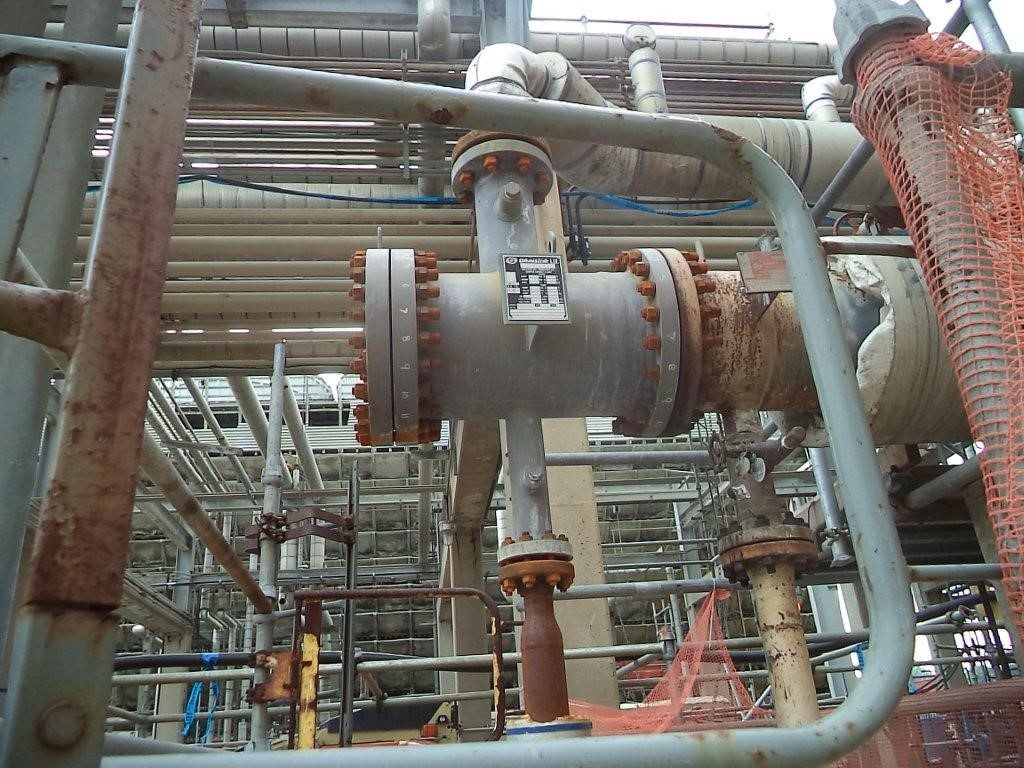
BOLTING ISSUE
A heat exchanger in service for about 20 years which has always been a notorious “leaker”. Before this installation, this heat exchanger would leak after every cycle.
Faulty heat exchangers can cause expensive, dangerous problems to occur, such as:
- Environmental hazards via spillage of low to mid levels of toxic pollutants
- Reduced airflow issues and inadequate pressure
- Expensive damage to machinery, such as cracks and microfractures
- Dangerous heat loads and high temperature fluctuations from faulty heat transfer
- Damage to seals
- Accelerated corrosion due to reduced service life
- Slowed operations from restricted flow
- Microbiological growth
SOLUTION
Supply bolts with Valley Forge SPC4 ™ Load Indicating Fasteners instead of standard conventional studs. Installers relied on load, reading directly on each stud as torque was applied.
Rechecks were done after all fasteners were loaded and ones out of range were tightened back into range.
Perfect load on each fastener was achieved before putting the heat exchanger back into operation. The bolts were used in combination with Lamons’ Corrukamm gasket and Belleville washers.
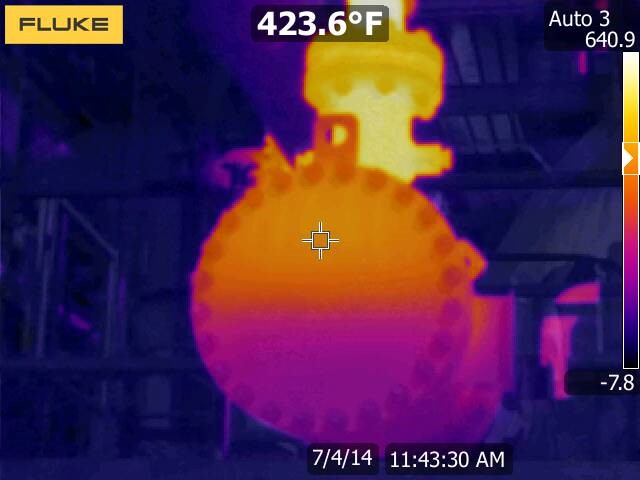
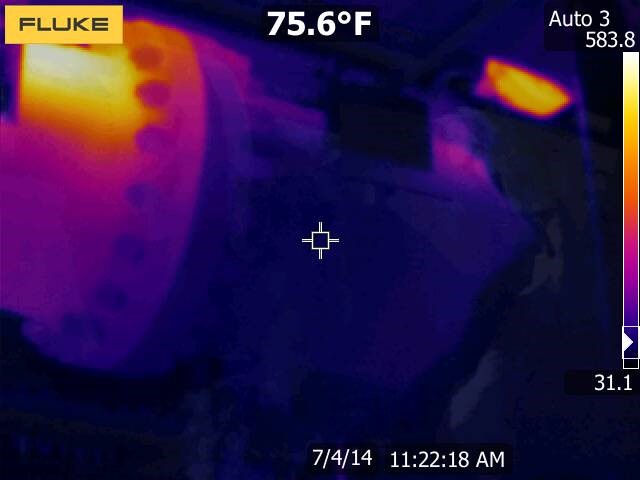
INSTALLATION
OUTCOME
After 22 thermal cycles on this exchanger, unit does not leak anymore!
In the 20 years prior to load indicating fastener installation, there had not been a single cycle without leakage.
Cost of fixing this leak issue on exchanger resulted in the amount of approximately $213,000 savings.
Savings was measured over previous 4-5 year time period.
The loss over the entire 20 years was not extrapolated; nor were maintenance costs.
The loss is calculated from the exchanger leak rate of 600 pounds steam and isobutane.