APPLICATION:
Autogenous Grinding Mill
LOCATION:
South Australia
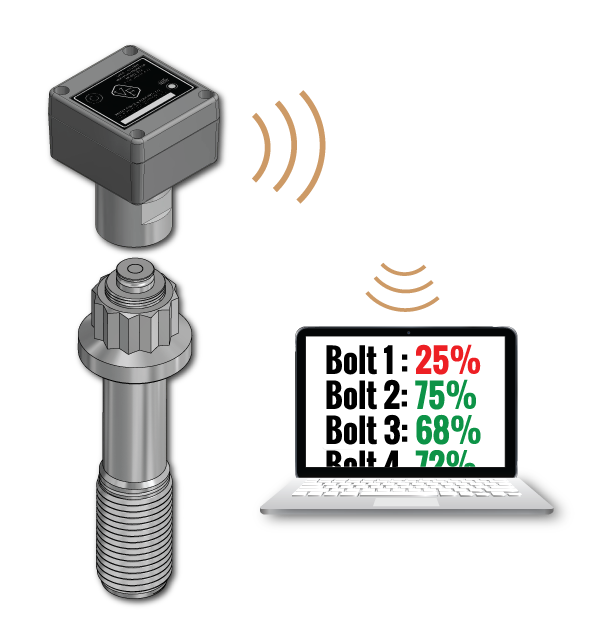
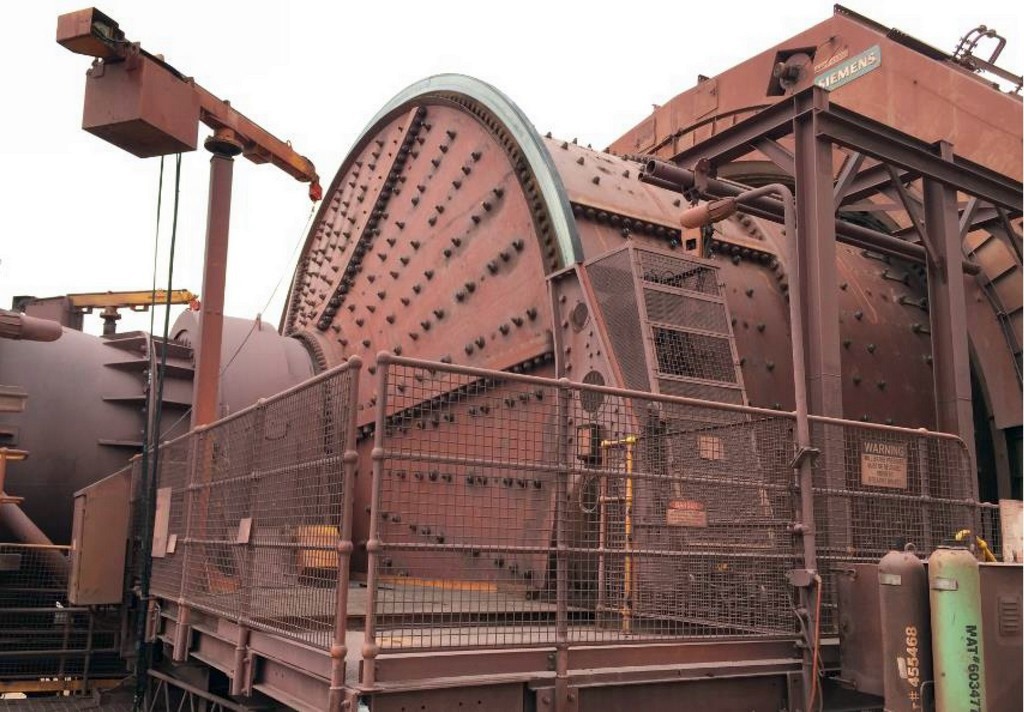
BOLTING ISSUE
Routine manual monitoring and maintenance of loose bolts on the grinding mills has been an industry standard. This process is time consuming involving down time, the company decided to improve safety and productivity with better use of technology. Due to the severe service conditions present in large grinding mill applications, the fasteners used to assemble the mill shell are considered “critical fasteners” and must be manufactured and maintained as such. This includes scheduled maintenance of the fasteners themselves, to ensure proper clamp load is being maintained in each joint. Traditionally this is done using ultrasonic elongation measurement technology, however this must be done during a scheduled outage and requires trained personnel to accurately interpret the results. Ultrasonic measurement also fails to provide the operator with real-time bolt load information.
SOLUTION
Replaced the radial flange and trunnion bolts with the Valley Forge & Bolt Mfg. Co. patented SPC4™ load verifying fasteners, on both the feed and discharge ends of the mill per the OEM’s specifications. Along with SPC4-404A electronic load readers, SPC4-500A mechanical load readers and SPC4-702 wireless transmitters, designed to provide real-time bolt load directly to the sites mill monitoring control room.
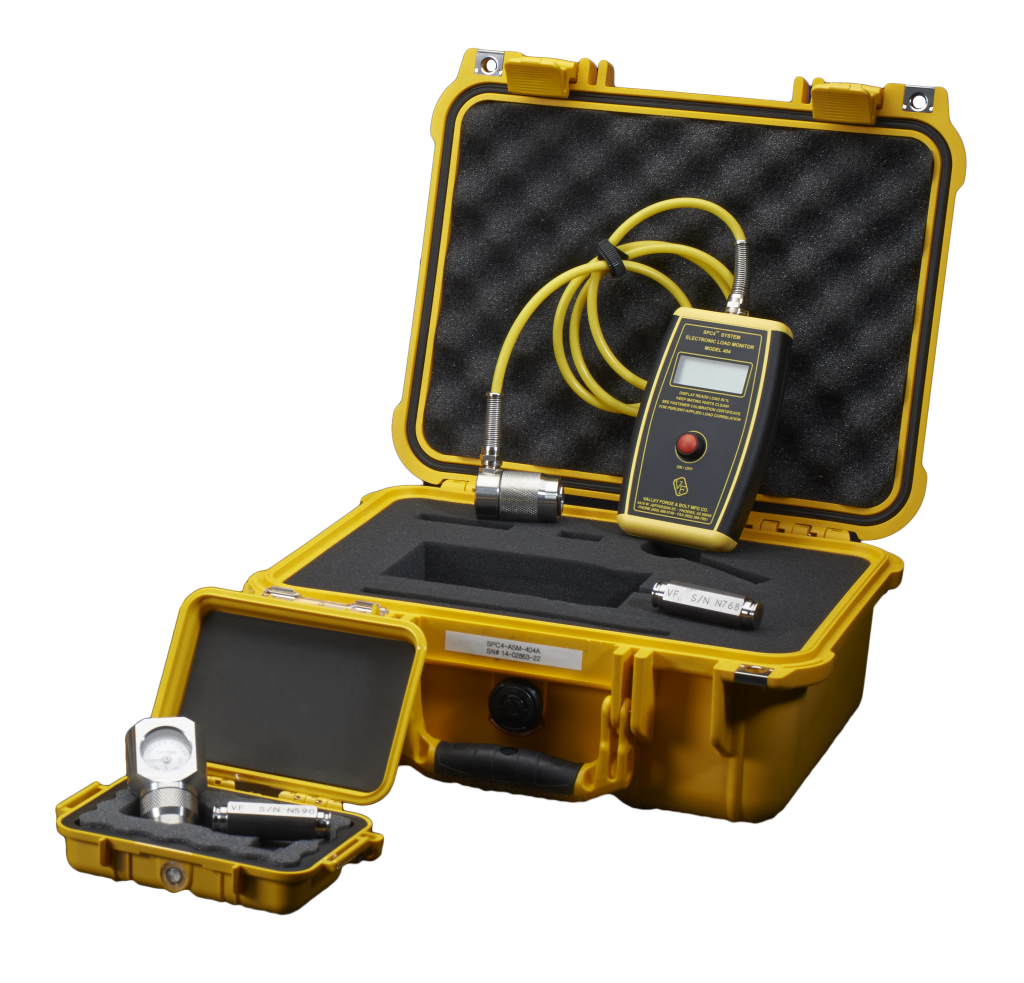
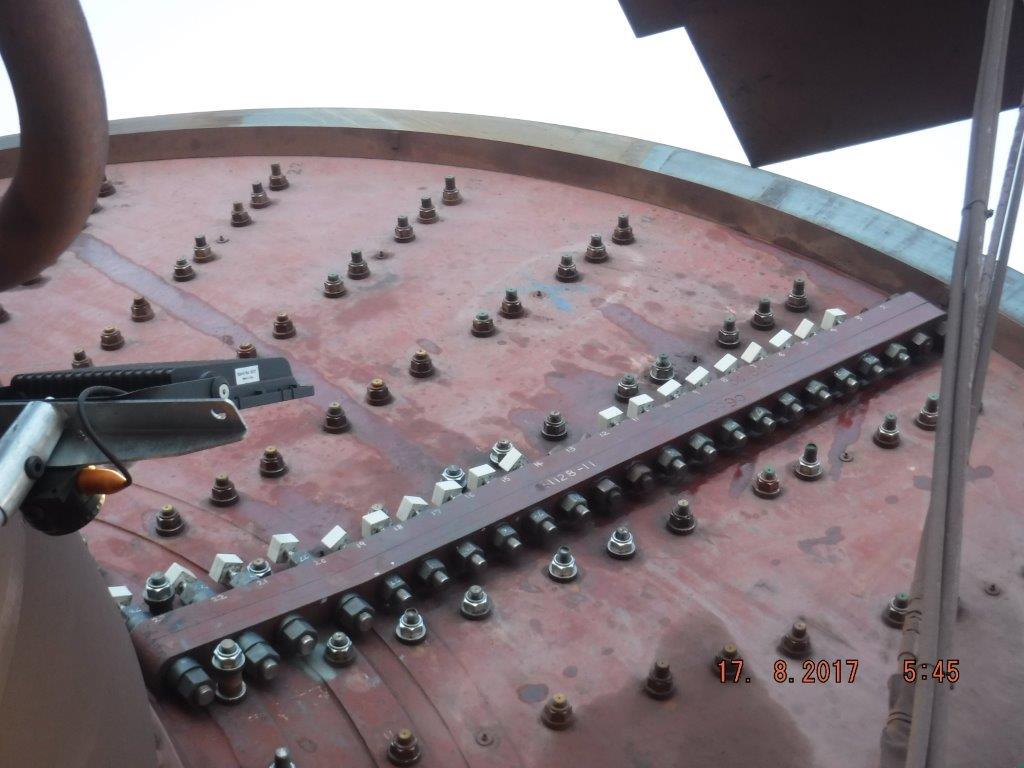
INSTALLATION
Through the use of Valley Forge’s patented SPC4™ technology, including the SPC4-404A and SPC4-500A load readers, the installation crew was given the ability to instantly verify that the clamp load in each fastener met the original manufacturers specifications. Once installed, each fastener was fitted with an SPC4-702 wireless transmitter, designed to provide real-time bolt load information to the sites mill monitoring dashboard.
OUTCOME
Using the patented SPC4™ load verifying fasteners and calibrated installation method has allowed the operators to monitor the direct tension within the bolt, alerting operators to the smallest loss of tension in real-time to immediately investigate, diagnose and prevent equipment failure while in the comfort of the control room . This valuable information gives engineers the chance to more effectively plan costly downtime.
Read more about this story on the Australia’s Mining Monthly.