APPLICATION:
Wheel and track sander nozzle bracket bolts.
LOCATION:
North Dakota, USA
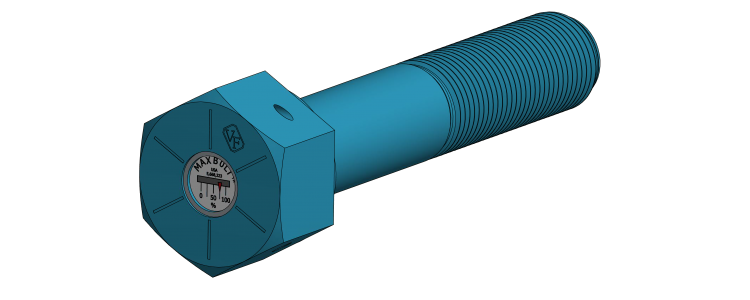
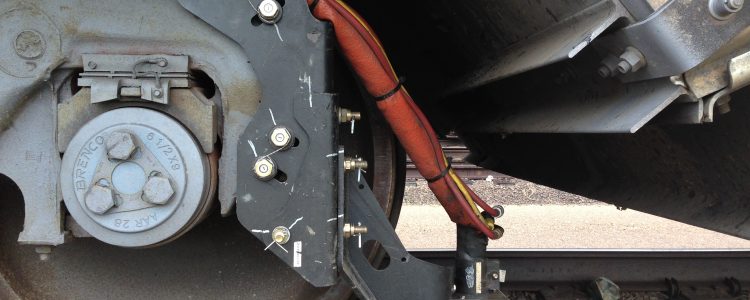
BOLTING ISSUE
Constant loosening from vibration resulting in bolt breakage, which is especially hazardous within the railcar industry. Bolt breakage can result in catastrophic equipment damages, it and poses enhanced risks to public safety.
SOLUTION
Maxbolt™ Load Indicating Fasteners: Proved out bolt load loss during operation which required retorque. After multiple retorques, Bolts settled, overcoming embedment and vibration loss resulting in no more loose or broken bolts.
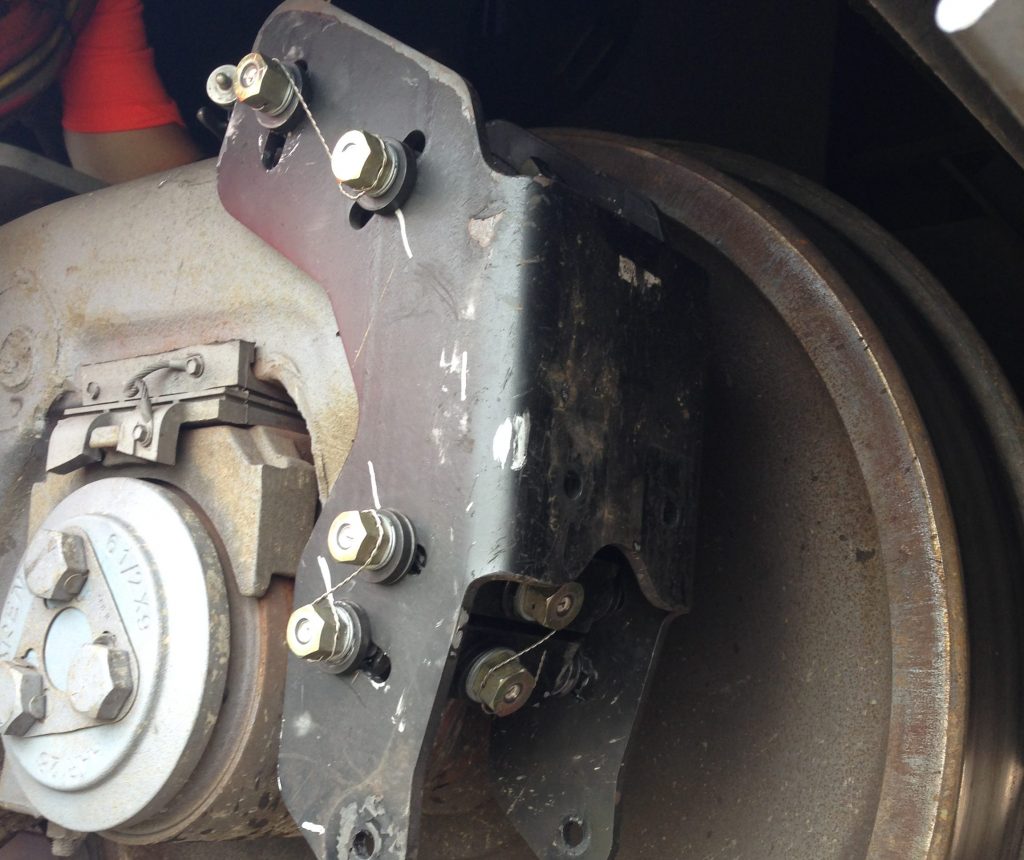
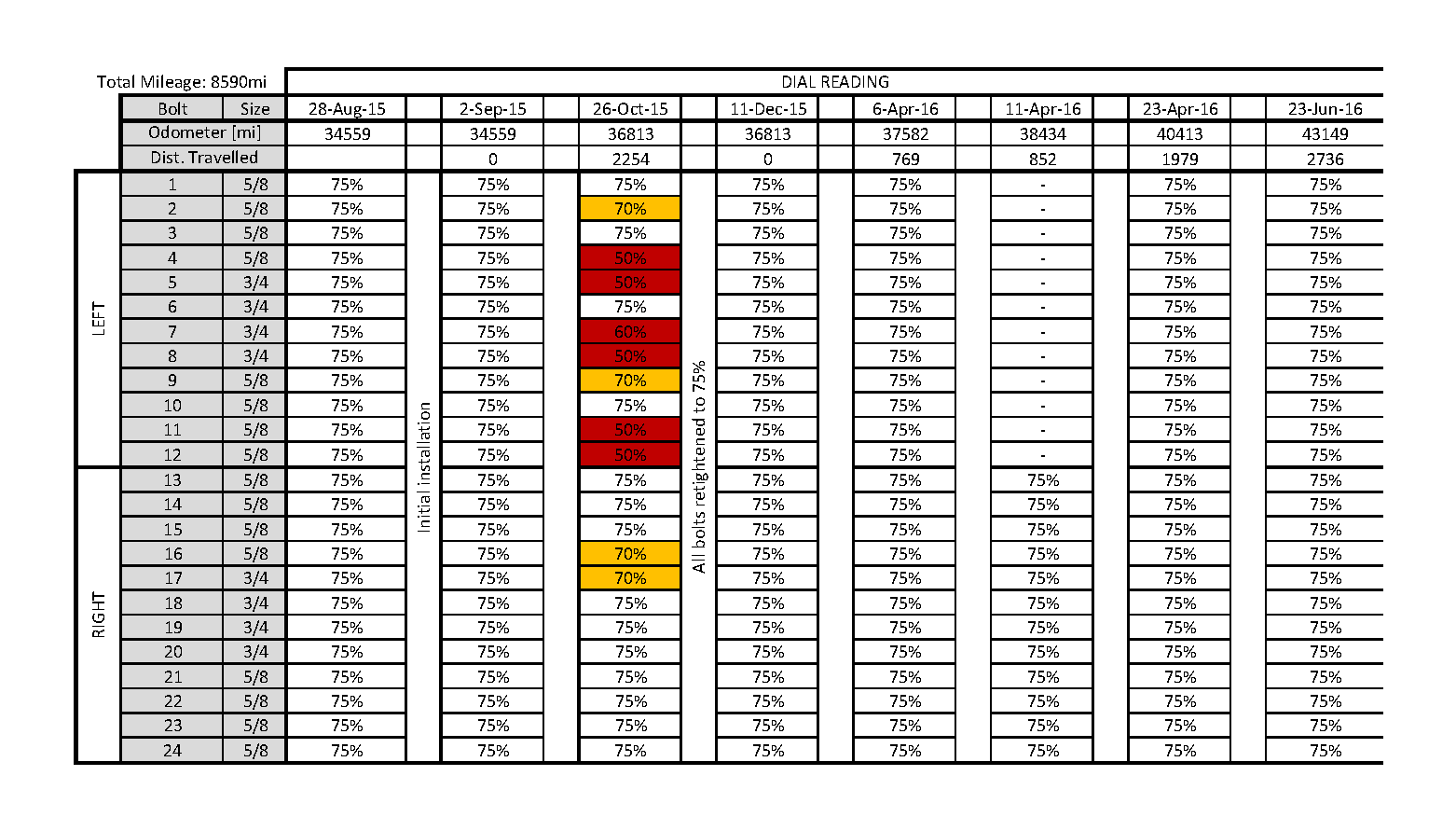
INSTALLATION
A bracket was retrofitted to the railcar axle. The assembly consisted of four bolted bracket mounts retrofitted to the axle and the bracket then fastened to the mounts. The whole assembly used a quantity of twelve — four 3/4” and eight 5/8” Maxbolt™, load indicating fasteners. Field Tests were performed by OEM on the Maxbolt™ load indicating fasteners by gathering data from two brackets bolted on to a right and left, car axle. All twenty four Maxbolt™ load readings, against railcar miles traveled, were measured during a ten month period, at the time of printing.
OUTCOME
Specifically with this OEM’s railroad bolting assemblies, safety is a first consideration.
For this application, Valley Forge’s Load Indicator Technology not only assures this safety with an accurate and instantly readable assembly preload, but also ensures quick maintenance, with no further need for routine retorqueing, other than those individual bolts reading low on the Maxbolt dial. Load indicating bolts are not for all applications but their ability to read accurate bolt load at a glance or during tightening, makes it ideal for this critical bolted assembly.
The quantitative clamp load readings displayed for this test, would have been by any other method, difficult and extremely expensive, if not impossible to obtain, without the Valley Forge Maxbolt™ Load Indicating System.